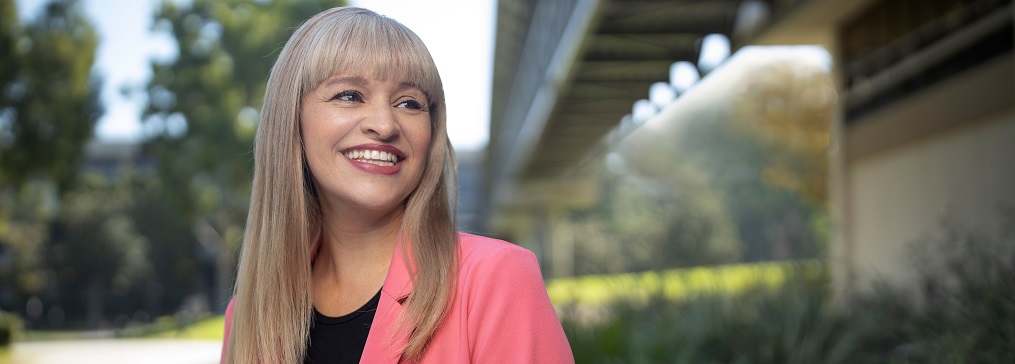
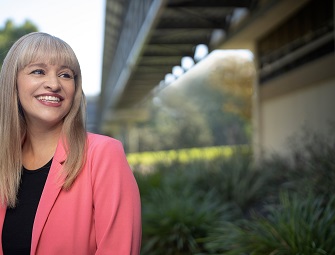
EVERYONE HAS A STRENGTH.
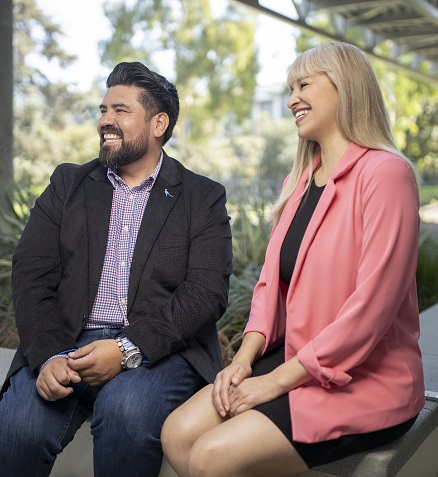
“EVERYONE HAS A STRENGTH, FIND IT IN YOURSELF, OTHERS, AND CREATE TEAMS THAT COMPLEMENT THOSE STRENGTHS TO ACCOMPLISH A COMMON GOAL.”
Lupe started her career at Edison in 2010 on a temporary assignment while she was working towards completing her bachelor’s degree in Business Information Systems & Technical Management. Before the completion of her assignment, Lupe transitioned into a full-time position in the Distribution Engineering Generation Interconnections department within SCE’s Transmission and Distribution organizational unit. In her current role, Lupe mentors other SCE employees in Continuous Improvement and Lean Six Sigma methodology. She runs improvement projects for her organization and is the Program Manager of the X-Change Program where she helps other employees implement their improvement ideas. She co-founded X-Change and was the acting Program Manager years before the role officially existed. Lupe has also led projects reducing lead time for processing renewable energy interconnection requests, resulting in shorter lead times from over 90 days to five days, and in some cases, same day service.
Her journey as a trailblazer for process improvement wasn’t easy. The challenges she experienced at SCE involved cultural resistance to embracing change and fear of failure when trying something new. She shares, “I had initially thought I had made a mistake in accepting a position with SCE and that perhaps I would not be a fit for the culture. However, I believed in the company’s mission and I was able to see it as an opportunity.” One of the opportunities she seized was finding like-minded team members across the company who embraced the idea of continuous improvement and created a program called the X-Change Program.
This effort empowered other SCE employees to safely test their innovative ideas and provided support if they encountered change-adverse behavior. Ultimately, what drives Lupe most are the people she works with. Lupe shares, “I’m very fortunate to be able to help others implement their improvement ideas and I get to coach and mentor employees in the process of becoming Lean Six Sigma Yellow Belt certified.” The advice she shares with many of her team members is that “everyone has a strength, find it in yourself, others, and create teams that complement those strengths to accomplish a common goal.”
We asked Lupe a few questions about her advice and career at Edison:
What’s your #1 piece of advice for candidates who are looking for jobs right now?
More than ever before, hiring managers are looking to align values as one of the deciding factors. Make sure you focus on giving examples about how you align with the company’s values.
How would you describe Edison’s support of continuous improvement initiatives?
Edison is focused on Continuous Improvement more than ever before. The company is on a two-year journey of embracing problem-solving based on Lean Six Sigma methodology and invests in building capabilities to sustain Continuous Improvement.
What type of training and programs does SCE have to support “continuous improvement?”
X-Change is an employee engagement program where participants identify and lead an improvement process leveraging basic continuous improvement techniques. It’s a great place to make new connections and network with like-minded individuals. X-Change has made a big difference in helping shape our existing culture of Continuous Improvement. As for training, we have several certification programs.
- Yellow Belt Certification – become a Kaizen facilitator using Lean Six Sigma focused tools to address common problems with minimal data analysis required.
- Green Belt Certification – learn how to lead mid-size improvement projects using slightly more advanced Lean Six Sigma techniques, data analysis, and light project management skills.
- Black Belt Certification – lead complex cross functional projects requiring advanced Lean Six Sigma techniques, data analysis, and project management skills.